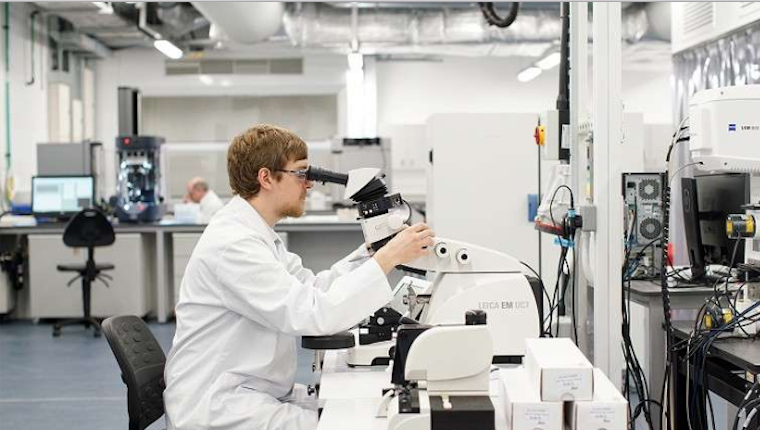
CPI Collaborates with Edinburgh University on Project to Create Digital Twin
CPI has created a cutting-edge, next generation system to drive efficient learning for complex particle products.
CPI, along with the expert input of its partners, has successfully coupled together two of its core projects – Models MPP and Prospect CP – to develop a novel, accessible Digital Twin. This facility creates an open-access learning environment to work against the challenges of powder mixing and granulation for solid products.
A Digital Twin can be defined as a learning system that combines a physical process asset with the virtual or digital environment, which allows model-based predictions of products to be produced on that real asset.
CPI’s Digital Twin is using a productivity enhancing approach, coalescing a twin screw granulator – and a coupled DEM (EDEM platform) and PBM (PSE platform) predictive model, which have been developed by the Universities of Edinburgh and Sheffield.
This combined toolkit, including modelling and the physical assets, enables an improved understanding of the product and process by coupling together different types of predictive models. This lets users quickly and cost-effectively refine and optimise production and set-up conditions prior to the commencement of highly complex real-life trials.
CPI’s Complex Particles capability allows real-time measurement to enable model validation and verification. It also creates the possibility for model-based control manufacturing, with both of these capabilities developed as part of the strategic project portfolio at CPI’s formulation facilities.
Dr Graeme Cruickshank, Director of Formulation at CPI, said: “These projects are exciting developments in the application of digital design methods to the development of formulated products and manufacturing process.
“The leveraging of UK expertise across industry, academic centres of excellence and highly-specialised technology suppliers has been key to the success of this project and will provide state-of-the-art capability to help UK companies benefit from developments in digital manufacturing.”
Professor Jin Ooi, from the University of Edinburgh, said: “We are delighted to have this excellent opportunity to work with industrial users and software providers to translate our latest particle-scale models to support industrial innovation in particulate products and processes.
“The resulting model-driven framework demonstrates how the predictive models that capture the correct physics of the problem, coupled with physical measurements, can support a digital transformation of industrial particulate processes.”
Professor James Litster, from the University of Sheffield, said: “We have been delighted to work with CPI, the University of Edinburgh and our industry colleagues to develop this Digital Twin.
“The project drew on the University of Sheffield’s well-established expertise in modelling particulate systems, and is well aligned with our strategic research theme of Smart Manufacturing of Formulated Products.
“It was particularly satisfying to work in close co-operation with commercial software developers, as well as industry end users, in the development of the Digital Twin.”
At present, the Digital Twin can inform standard processing, by delivering an understanding of the experimental starting point in the key area of high-value complex solids, such as those used to create pharmaceutical tablets. In future, it will enable flexible, real-time control and high-quality manufacturing for a much broader range of high-value products.
The work has been made possible through funding from Innovate UK and collaboration with project partners, which include AstraZeneca, EDEM, Johnson Matthey, Pfizer, PSE, Procter & Gamble, the University of Sheffield and the University of Edinburgh.