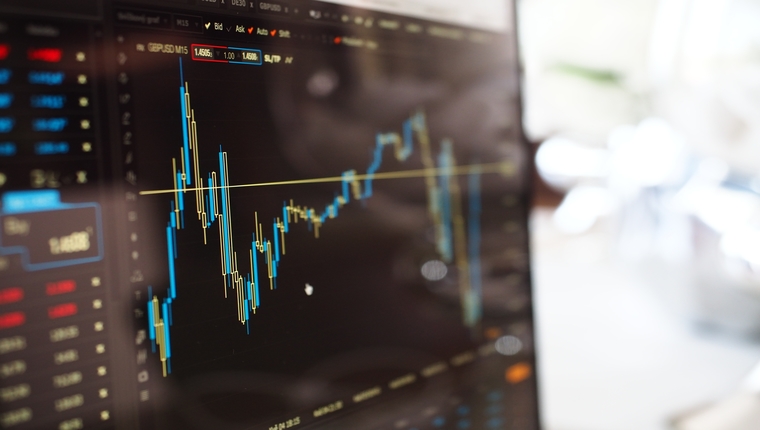
Demystifying Digital: Data for Digitalisation
During 2019, several individuals from the Life Sciences sector in Scotland came together to prepare a series of workshops and lectures on how digitalisation is creating opportunities in Life Sciences.
Working closely with Scottish Enterprise and the Life and Chemical Sciences Manufacturing Strategy Steering Group, the team looked particularly at digitalisation for manufacturing processes. Two of the team members, Michelle Waddell and Rob Innes of Wyoming Interactive looked at how data is used to create value in a digital transformation project. This post picks out some of their observations on the series.
Data for Digitalisation
Data, it’s fair to say, is all around digitalisation projects. In fact, there is no digitalisation without data as it flows everywhere — from sensors and instruments to control systems, resource planning systems, back through supply chains to third party vendors and onward to customers.
Data is used at every point in the manufacturing process and there are many opportunities to improve and extend the use of data. Michelle and Rob looked at the following areas in particular.
- Assessing the data available and how to maximise it
- Abstracting data sources from reporting platforms
- Visualising data and reporting dashboards
Assessing Available Data
Most organisations will acknowledge that data from different machine configurations, data from different vendor systems and data from different processes can present in incompatible formats, making comparison and decision making challenging.
In speaking with manufacturers, the idea that extensive data assets existed but were difficult to get at or difficult to organise, really resonated with attendees.
Whilst the individual actions to improve data uses will reflect the particular situation of each organisation, starring with an audit / assessment is a good place to start. Find out where data exists, how it’s collected, what format it’s in and what data governance operates on the source (do different sites or different teams operate different standard operation procedures)?
An assessment won’t fix anything, but it will tell you what needs to be fixed. A priority can then be attached to each source. And it will start to shine a light on data opportunities.
Abstracting Data Sources
Abstraction is very helpful in managing multiple data sources (and accommodating data sources that you have no visibility of yet, for example, for emerging technologies). Simply put, abstraction means separation. Separating some finance reporting from finance systems, separating inventory reporting from inventory systems, separating packaging reporting from packaging systems, etc.
Taking data events from different sources into a horizontal data platform (that spans all sources) will create opportunities for cross functional analysis and reporting. As sources are integrated, the data stream from each one may undergo conditioning (to address quality issues) or normalisation (to address inconsistencies in naming, coding, units of measure, etc).
Doing this work means many of the differences between sites, suppliers, instruments and so on can be removed and a view across the organisation provided, greatly improving data for decision making.
Visualising Data
With a clean base of integrated data, horizontal reporting is available and one of the common presentation methods is a dashboard. Rather than circulating a pdf or an excel file (where the data view and the chart move together), dashboards connect to a data hub, the horizontal view across sources, and provide a rich visual framework to express the data analysis, independent of the data hub.
Dashboard tools like Google Data studio, Power BI, Tableau and many others are rich tools to connect several sources and create dashboards that benefit from these key features:
- Interactivity
- Near real-time data
- Personalisation
For some processes, the data is so complex, so voluminous or the onward use is so complicated that custom visualisations are required. These require expert help but model or illustrate patterns and trends previously hidden. Custom visualisations can yield very positive outcomes for teams.
Summary
This is a brief look at the data element to Demystifying Digital. Those attendees who took park in the workshops found that the scenarios presented reflected their real-world challenges and they appreciated the suggestions. Hopefully they took them back to their organisation and realised some benefit.
If you would like help, ask the Scottish Life Sciences community via contact us here or via our LinkedIn company profile